Packaging is one of the fastest-growing industries, with a global value of USD 700 billion. Plastics are being used in the packaging of materials such as food, beverages, oil, and so on. Plastics are used extensively due to their performance, cost-effectiveness, and durability. The plastic packaging market grew at a 3.47 percent CAGR from 2021 to 2026.
However, there are several challenges and risks faced by the plastic packaging industry today. High inflation and rising prices, a lack of skilled workforce, difficulty obtaining raw materials due to insufficient infrastructure, growing environmental concerns, efficient recycling of mixed plastic waste, and many more are some of the issues facing the industry.
Most often organizations are hardwired to consider factors such as the product’s quality, usability, and benefits. This frequently takes the focus away from the packaging. In some cases, businesses are unaware of how their packaging affects them. Thus, to make organizations aware of the market trends and to enhance efficiency, Faber Infinite has devised tools like Inventory management, Single Minute Exchange of Dye (SMED), Total Productive Maintenance (TPM), Overall Equipment Effectiveness (OEE), Mean Time Between Failures (MTBF), Mean Time to Repair (MTTR), Time & Motion Study, and others. These are some of the methods for developing structured manufacturing facilities and profitable businesses.
Food packaging, which is a major consumer of plastics, is increasingly replacing traditional materials such as paperboard, metals, and glass with more advantageous properties such as plastics due to its lightweight and low-cost benefits.
One of the clients in the plastic packaging industry had collaborated with Faber Infinite Consulting for efficiency improvement, changeover time reduction, and productivity improvement across various sections of manufacturing as part of the continuous improvement journey.
The tangible benefits delivered to the client from the plastic packaging industry during their improvement journey are:
- Productivity has increased by 37%.
- Throughput Time is reduced by 30%.
- Changeover Time is reduced by 30%.
- Quality has improved by 25%.
- Manpower costs are reduced by 35%.
Productivity increases not only contribute to overall industry production but also help to increase competition and innovation in the market as a whole. Another key area where improvement can impact the organization’s resilience and agility.
- Inventory Management & E-Kanban
- Decreased Changeover Time
- Rework reduction
- Increased overall equipment effectiveness
- Decreased performance during extrusion
Plastic consumption has skyrocketed as the significance of plastics in our lives has become undeniable. They are the essential foundation of most medical equipment and safety gear, keeping our medical systems running.
As a result of Team Faber’s contribution to the plastic packaging industry, we are glad that our clients have been able to build a sustainable and competitive market.
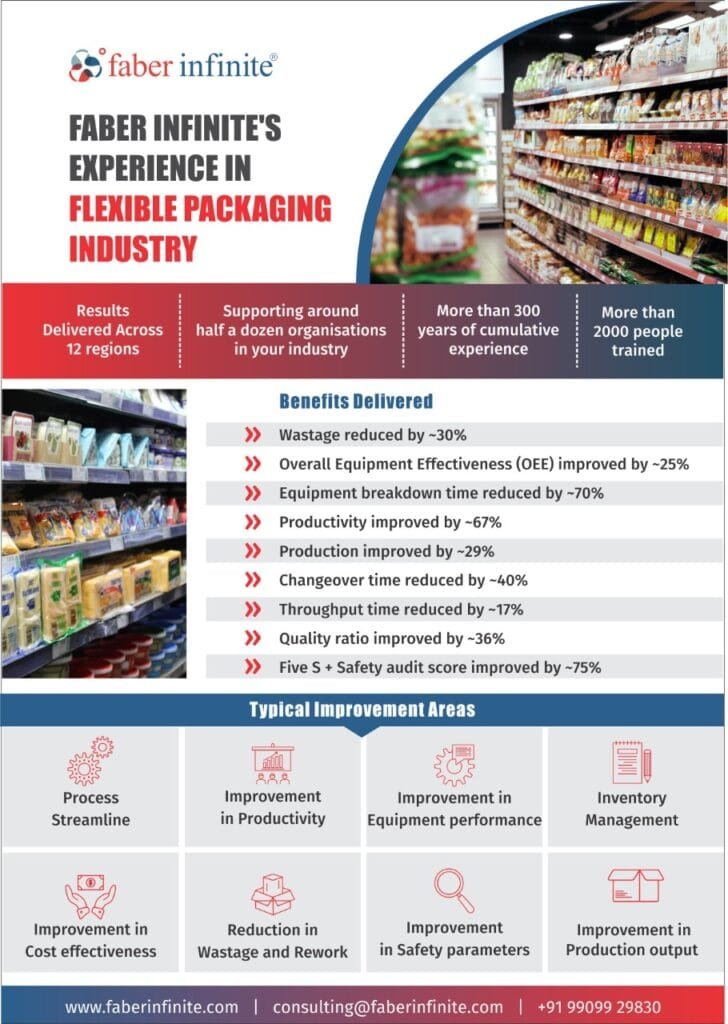
Contact us today to receive the best-in-class methodology from Faber Infinite Consulting’s expert consultants.
Ready to lead the way in the plastic packaging industry? Fill out the form below to unlock valuable insights and strategies for building sustainability and staying ahead of the competition. Don’t miss out on this opportunity to secure your future in the ever-evolving world of plastic packaging!
Written by Faber Aleena & Compiled by Faber Mayuri